சுருக்க குழிக்கு மிக அடிப்படையான காரணம் என்னவென்றால், அலுமினிய கலவை திரவத்தில் சுருங்கி கெட்டியாகும்போது, சிலிக்கா சோல் துல்லிய வார்ப்பு தொழிற்சாலை, வார்ப்பின் ஒரு குறிப்பிட்ட நிலை (பொதுவாக இறுதி திடப்படுத்தல் இறுதியாக திடப்படுத்தப்படும் சூடான இடம்) திரவத்தைப் பெற முடியாது என்பதைக் கண்டறிந்தது. நேரத்தில் உலோக உணவு, அதனால் ஒரு சுருக்க குழி அந்த இடத்தில் உருவாக்கப்படுகிறது.
கார்பைடு அலுமினிய உலோகக்கலவைகள் அல்லது அலுமினியம் கலவைகள் குறுகிய திடப்படுத்தல் வெப்பநிலை வரம்பில், செறிவூட்டப்பட்ட சுருக்க துவாரங்கள் வார்ப்புகளில் ஏற்பட வாய்ப்புள்ளது. அலாய் கலவை அட்டவணையில் இருக்கும் போது, சுருங்குதல் குழி பொதுவாக வார்ப்பின் சீரற்ற தடிமன், அதிக சூடான மூட்டுகள், அதிகப்படியான, வரிசையான திடப்படுத்தலுக்கு உகந்ததாக இல்லாத, கொட்டும் ரைசரின் கட்டுப்பாட்டு அமைப்பின் நியாயமற்ற வடிவமைப்பு ஆகியவற்றால் ஏற்படுகிறது. சிலிக்கா சோல் துல்லிய வார்ப்பு பாகங்களின் சூடான மூட்டுகளை உருகிய உலோகத்தால் நிரப்ப முடியாது. அல்லது கொட்டும் வெப்பநிலை மிக அதிகமாக உள்ளது.
தவிர்க்க வேண்டிய எதிர் நடவடிக்கைகள்:
1: சீரான தடிமனை உறுதிப்படுத்த, வெப்ப மூட்டுகளைக் குறைக்க அல்லது ஒழுங்கான திடப்படுத்தலுக்கு உகந்த தடிமன் மாற்றங்களைச் செய்ய வார்ப்புகளின் கட்டமைப்பை மேம்படுத்தவும்.
2: ஆர்டரை உறைய வைக்கும் வகையில் ரைசர் அமைப்பை திறம்பட அமைக்கவும். பல ஹாட் ஸ்பாட்கள் கொண்ட சிக்கலான பகுதிகளின் ஊற்றும் ரைசர் அமைப்புக்கு அதிக கவனம் செலுத்தப்பட வேண்டும்.
3: சிலிக்கா சோல் துல்லியமான வார்ப்பு பாகங்களின் கீழ் ஒரு குறிப்பிட்ட தூரம் இருக்கும் வகையில், பகுதி வெப்பச் சிதறலின் சிரமத்தைத் தவிர்க்க, தொகுதிகளை திறம்பட இணைக்கவும்.
4: ஷெல் மற்றும் உருகிய உலோகத்தின் ஊற்றும் வெப்பநிலை பொருத்தமானதாக இருக்க வேண்டும், மேலும் கொட்டும் வெப்பநிலை மிக அதிகமாக இருக்கக்கூடாது
5: ஊற்றும்போது, ஸ்ப்ரூ மற்றும் ரைசர் உருகிய உலோகத்தால் நிரப்பப்பட்டிருப்பதை உறுதிசெய்து, ஸ்ப்ரூ கப் மற்றும் ரைசரில் வெப்பமூட்டும் முகவர் மற்றும் வெப்ப காப்பு முகவர் சேர்க்கவும்.
6: உருகுதல் மற்றும் செயலாக்கத் தொழில்நுட்பத்தை மேம்படுத்துதல், உருகிய உலோகத்தில் கழிவு வாயு மற்றும் உலோக ஆக்சைடுகளைக் குறைத்தல் மற்றும் சுழற்சி மற்றும் உணவு அளவை மேம்படுத்துதல்.
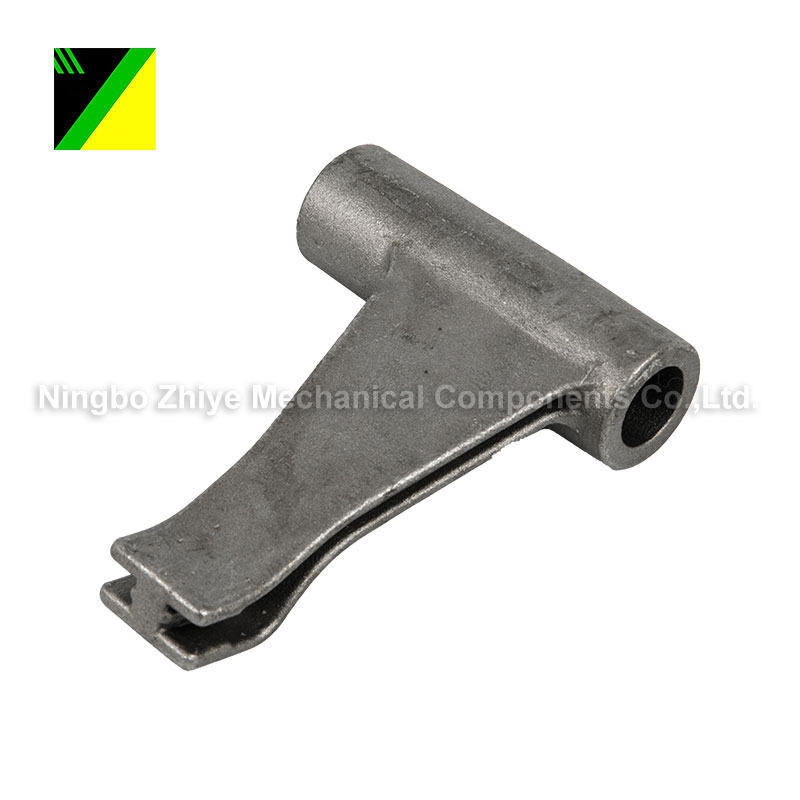